In June 2021, CoreDux appeared in the Château-Thierry. The article was in French. For our English readers, we hereby offer the interview in English.
CoreDux designs and manufactures flexible hoses, most often made of stainless steel. These are notably used in space launchers, electric cars or for microprocessor production.
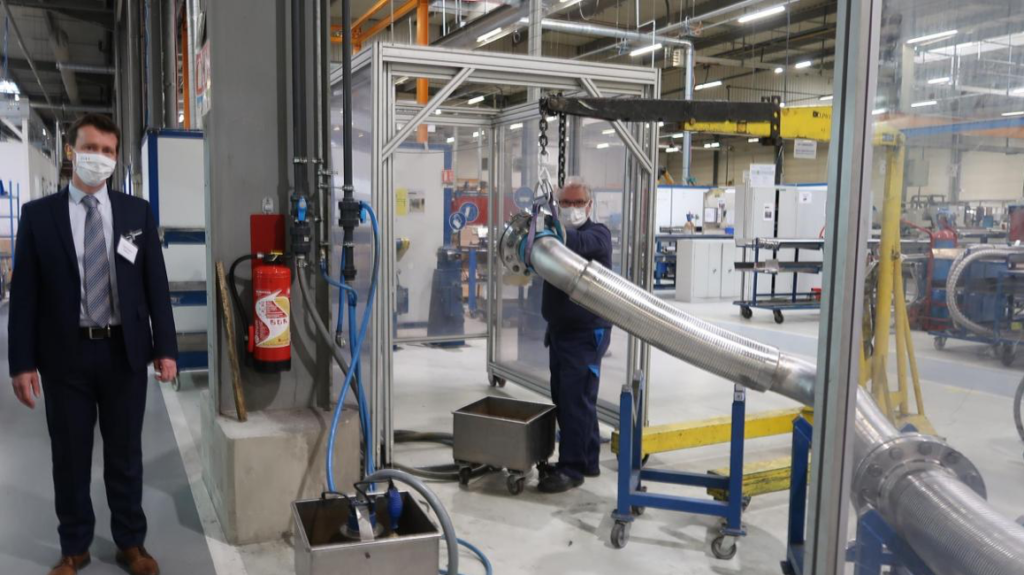
The essentials
CoreDux, situated in the Omois activity park, in Epaux-Bézu, since 2014, at one time known as Boa Flexible Solutions, was initially part of the Boa group, before leaving it in 2019.
CoreDux designs and manufactures artery solutions for fluids and gases. These are hose systems, mostly made of stainless steel, resistant to extreme temperatures or pressures.
Semiconductor, Aeronautics, Space, New Energy and High Tech are the four main sectors where the products of CoreDux make a difference.
Tailor-made solutions
Braided or corrugated, large or small, short or long, the flexible hoses produced by CoreDux are very diverse but unique and destined for a brilliant future. Some of the products even find their place within the Ariane launcher, be it for the propulsion system or for cooling systems. The specificity of these fluid and gas transfer solutions is to withstand extreme temperatures or very high pressures.
This company is a gem, we are at the crossroads of everything which concerns the future of humanity.
Julien Fauquenoy, Managing Director CoreDux France
Industry challenges
Flexibility, leak tightness, resistance to extreme temperatures and pressures, but also fatigue resistance are the qualities of these hoses that look like boas, resemblance to which the group’s original name referred to when it was located in Fère-en-Tardenois and again when it settled in Épaux-Bézu, in the Omois activity park, before becoming CoreDux. The new group consists of two companies, the first in the south of the Aisne region, employing about 150 people, the second, in Tilburg in the Netherlands, dedicated to purified solutions.
“We are an engineering company, we design fluid and gas transfer solutions”, explains Julien Fauquenoy, Managing Director. These hoses are often metallic, made of stainless steel, but can also be made of PTFE, a kind of plastic. The hoses and transfer solutions have inner diameter that can vary from 4 to 200 mm!
CoreDux mini-museum
In the factory or in the display cabinets, since a mini-museum has been inaugurated in the premises, visitors can discover how a strip, that is to say a metal plate, is rolled, welded and then preformed, to become the famous transfer solution, resistant and flexible, ideal for hydrogen, tomorrow’s source of energy. “All vehicles will use hydrogen in the future”, explains Julien Fauquenoy, the managing director, truly enthusiastic: This company is a gem, we are at the crossroads of everything which concerns the future of humanity.”.
Indeed, the aeronautics sector can use products manufactured in the south of the Aisne region, both for space launchers, such as Ariane 6, or satellites or launchpads. In addition “we are eminently part of everything that has to do with clean energy”, says Julien Fauquenoy, who insists on the fact that Coredux’s transfer solutions can allow an EV’s battery pack to last longer. They are therefore used for electric cars, but also, in clean mobility as a whole, for trains or HGVs.
Hoses from the south of the Aisne region travel far and wide!
CoreDux specific projects and growth
CoreDux, along with two other companies from the Aisne region, was awarded 1.5 million euros from the fund for the modernization and diversification of the aeronautical sector. “In order to meet the new requirements from the market, CoreDux has initiated a series of projects to digitalise its operations, to add to its machine park, to support the ongoing transition to new energies and to be a major player in the High Tech industry thanks to its ongoing product diversification,” the prefecture’s press release states. The prefect himself also visited the company to meet with the managing director and the employees.
There are currently 150 employees but the director indicates that CoreDux is recruiting, “we hire 10% more people every year”,he points out, mostly from the east of the Paris basin, or from Soissons, Laon and Reims.
Investments for the CoreDux machinery park and R&D department
To obtain this sum from the recovery plan, CoreDux presented a very detailed file and Julien Fauquenoy says he knows where this money will be used: “€800,000 to modernize the machinery park and allow to further miniaturise our transfer solutions”, explains the director. The objective is to propose solutions from 3 mm to gain in lightness, because “weight is the enemy of performance”. The remaining €700,000, will be “dedicated to R&D and innovation”, for example so that the piping solutions, ever smaller, achieve the same performance, despite, for example, vibrations in the atmosphere.