Fluid Containment
Perhaps the most important challenge in the transportation of mission critical liquids From Semicon to Space and Aeronautics, fluid containment is fundamental. Tackling this challenge is essential to prevent the risk of leakage, maintain pressure and ensure maximum performance. The answer to this challenge? Choosing the right components and good old-fashioned craftsmanship.Summary points
- CoreDux has developed a wide range of hoses tailored to specific purposes and constructed from various materials, including stainless steel, PTFE, PFA, THV, and PUR, carefully chosen to match the properties of the fluids they transport, ensuring optimal performance.
- An overall defect rate as low as 0.08% reflects our commitment to optimized design, craftsmanship and quality.
- Each product undergoes rigorous one-on-one testing, checking it 100% for leaks using up to seven different testing methods, including helium and water pressure tests, demonstrating CoreDux’s dedication to reliability.
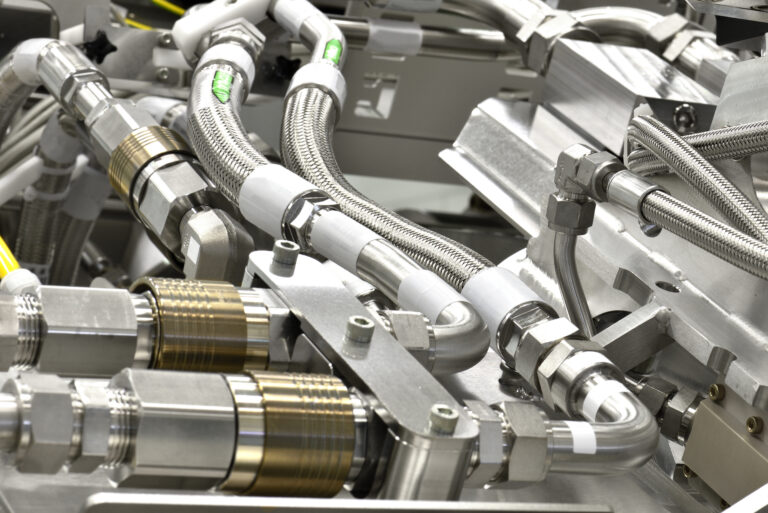
In the realm of high-tech manufacturing, precision is paramount. In industries like Semicon, Space, and Aeronautics, systems demand ever-greater precision, emphasizing the importance of fluid containment. Over the years, we have adapted to the evolving needs of our customers by developing a wide range of hoses tailored to specific requirements and constructed from various materials, including stainless steel, PTFE, PFA, THV, and PUR, carefully chosen to match the properties of the fluids they transport, ensuring optimal performance.
However, the challenge goes beyond material selection. Factors like temperature, pressure, flow speed, dampening properties and vibrations all influence the performance of these hoses. Essentially, our engineers are engaged in a sophisticated form of “plumbing” where every detail matters.
At the heart of this endeavour lies fluid containment, which is crucial for preventing leakages. Despite its apparent simplicity, leakages continue to cause billions in damages across industries. For CoreDux, guaranteeing uptime for clients is non-negotiable. With an overall defect rate as low as 0.08%, we believe it’s safe to say our craftsmanship matches this ideal.
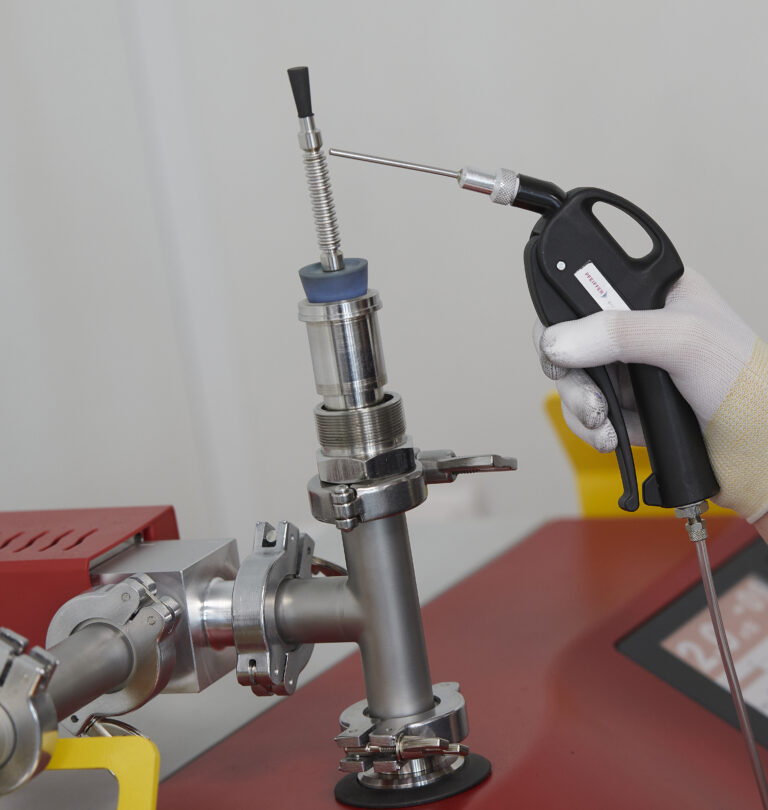
The challenges faced by our diverse clientele may vary, but the engineering requirements remain similar. Whether it’s transporting water for Semicon’s lithography or connecting fuel tanks to engines in Space and Aeronautics, the stakes are high. In industries where safety and reliability are paramount, any compromise in fluid containment could have catastrophic consequences.
That’s why testing is a crucial part of our process. Each product undergoes rigorous one-on-one testing, checking it 100 percent for leaks using various methods, including helium and water pressure tests. Leak tightness is not just a goal but a fundamental principle that permeates every aspect of our design and manufacturing process.
We understand the critical importance of uptime in industries like Semicon, where downtime translates to significant financial losses. Moreover, the collateral damage from leaks can be catastrophic, underscoring the need for reliable fluid containment solutions.
Where standardized components meet craftsmanship
In a world increasingly driven by standardization, we aim to consistently provide the right components with the same high standards. From design to production, we work closely with our clients to ensure the reliability and performance of our products. This involves selecting the right components and optimizing production processes to minimize leakage and improve overall product quality.
Ultimately, it comes down to the meticulous selection of components and a dedication to delivering quality solutions. Fluid containment is not just about preventing leaks; it’s about safeguarding the integrity of entire systems and, in some cases, even human lives. And for us, ensuring that every hose we produce meets the highest standards of our industry is not just a commitment but a mission.