Explaining our new cyclic nucleation cleaning technology
Cyclic nucleation cleaning. Fantastic for Scrabble, but a bit of a mouthful… That’s why we sat down with our colleagues Jonas and Sander. Jonas and Sander have been jointly responsible for implementing this new technology here at CoreDux, and they were more than happy to help us demystify this new tool. In this interview, we’ll tell you all about the features and the benefits that our new cleaning process brings to the table.
Good morning, gentlemen; let’s start with a quick introduction. Can you tell our readers a bit more about yourself?
Sander: Sure! My name is Sander. I’m a process engineer specialising in cleaning and cleanliness validation and the driving engineer behind the CNp project.
Jonas: And I’m Jonas, the project manager for the CNp Cleaning Project and responsible for the high-level aspects of this technology project.
What is the CNp cleaning technology? Can you explain it to us in layman’s terms?
Jonas: We are continuously searching for innovation within cleanliness, and with this new technology, we’ve upgraded our cleaning capabilities once again. This new tool is the first machine within CoreDux in which we can simply put products to clean inside, select a program, let it run, and products come out clean and dry. It gives us many options to create cleaning programs and lets us play with many parameters to clean products and components we couldn’t easily clean before.
That sounds exciting, but let’s dive a little bit deeper. How does CNp cleaning work?
Sander: This new cleaning tech is a big upgrade compared to conventional ultrasonic cleaning methods. It’s super effective, especially for tough-to-clean products. Here’s how it works: the items are cleaned in a closed chamber. The chamber is filled with a diversity of potential cleaning fluids and subjected to fast over and under-pressure cycles (which enables us to clean a diversity of array of contaminations). As a result, lots of bubbles are created on the product surface and, when imploding create a pulling force that removes particles and contamination from the products. It even reaches into every nook and crannies. In the past, several machines were required to get the same result, but with this optimization we now have a one-stop solution.
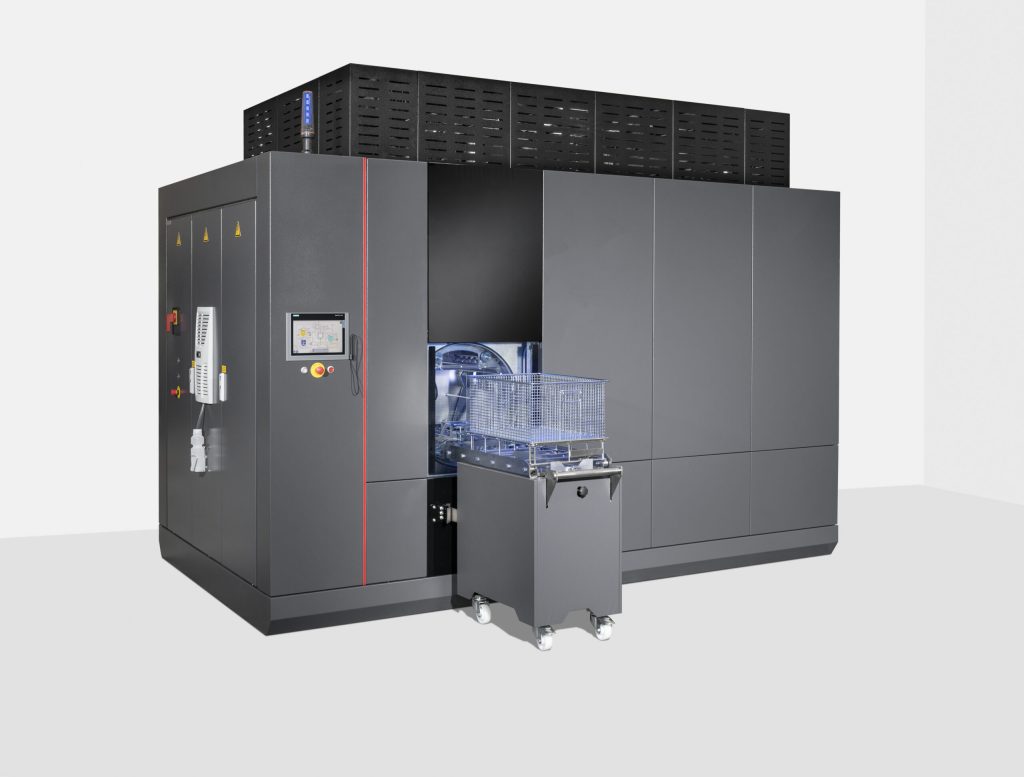
Why did we need this? What kind of benefits does it offer to our clients?
Sander: Let’s take our braided PTFE hoses range as an example. These are PTFE hoses with stainless steel braiding around the PTFE core hose. To create this braiding, you need lubricants like oil. We need these lubricants for the threads that go into the braiding and for the versatility of the hose, but cleaning those cavities in the braiding can be a challenge. You need a method that is sophisticated enough to go into those cavities. CNp Cleaning is such a method.
Jonas: The products to clean and customer cleanliness requirements are getting more and more stringent, especially in the High-tech industry such as Instrumentation and MRI systems. New products bring new challenges because of new materials that might be more sensitive or have other restrictions for cleaning. This tool is an innovation of our cleaning capabilities and widens the range of possibilities we have to answer customers’ needs. That’s why we made this investment. It’s our first CNp machine and more machines could follow if it proves as good as we think it is.
Sander: It’s definitely important for High-Tech, but we won’t stop there. The added value of this cleaning process is that it can handle complex products with small details. In Aerospace (engines and rockets), clean mobility (H2, Co2, and Air conditioning), and high-tech (MRI, Electron microscopy, Instrumentation), you can also run into that category of products where a high level of cleanliness is required. We expect to be using this for a lot of different industries soon!
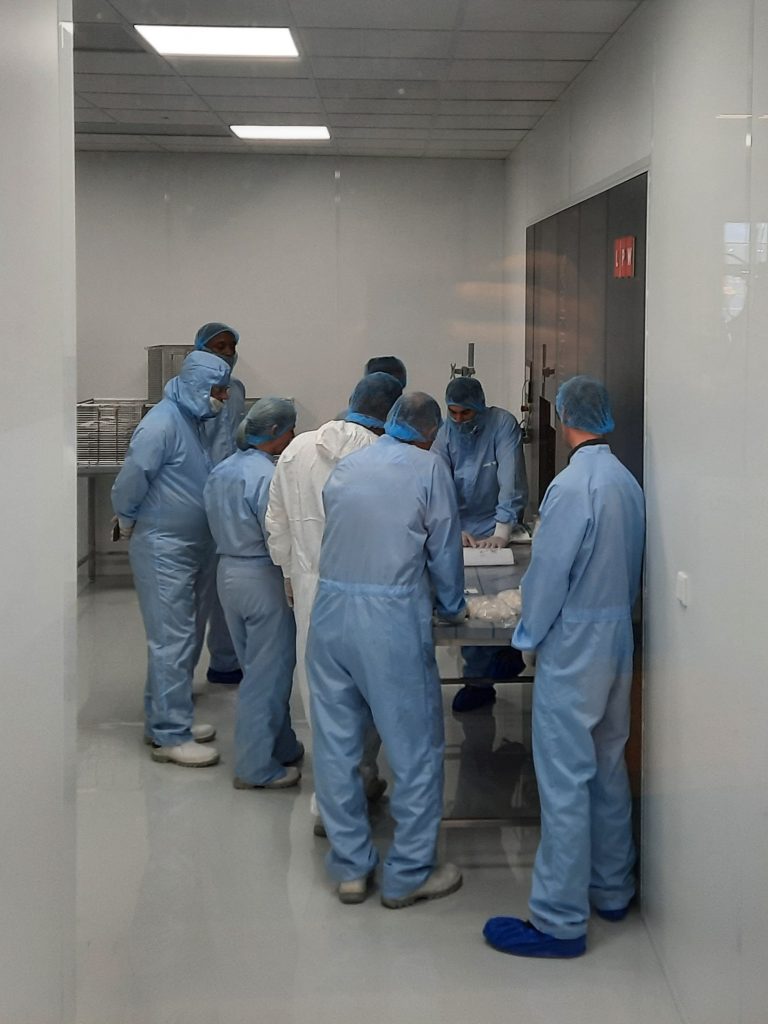
Sounds big. Do you have any numbers you could share on this machine?
Jonas: We can safely say the investment to implement such a technology, from feasibility study to the build of a separate cleanroom, is huge. And yes, It’s… ehm, a fairly large machine.
Sander: Yep, about the size of a school bus…
Jonas: How much does it weigh again?
Sander: A couple of tonnes without water. And even more with all tanks filled!
Sounds heavy. How long did it take to implement?
Sander: The lead time has been about two years. In 2021, we started a technology program to make sure we would stay on the forefront in the field of cleaning. That basically meant that we made an overview of all available technologies and a selection of what would be interesting for us to expand our installed equipment and techniques. Then, we did a feasibility study and made a selection of our hardest-to-clean products. We tested several technologies, and this one performed best of them all.
Any words of thanks or praise?
Sander: Certainly! I really want to thank CoreDux’s management for their willingness to make this investment. Moreover, I think our supplier did a stellar job. They’ve spent a lot of time on us doing tests and helping us make the best decision.
Jonas: I fully agree. Credits to Sander and the whole CX Team for making this happen over the last 2 years.
Then that’s that. Thank you, gentleman!
Sander and Jonas: You are welcome!
Are you as intrigued by CNp cleaning as we are, and would you like to learn more about this latest add-on to our technology portfolio? Jonas, Sander and our other engineering colleagues are happy to help. Just reach out to us by pressing the link below to learn more about CNp cleaning or other forms of cleaning.