As an all-in-one original design manufacturer and system integrator for gas and liquid transportation, CoreDux® designs and produces crucial artery systems, with the brand promise to bring your machinery to life. A core competence in the manufacturing of these vital connections is state-of-the-art welding expertise. And CoreDux® engineers have that skill in abundance, with extensive know-how in a wide variety of welding techniques. It is such vital capability that you could just as easily consider CoreDux® an advanced welding company, a.o. specifically qualified according NEN-EN ISO 3834-2. Extensive investments in welding automation keep the company at the forefront by extending its welding capacity to satisfy growing customer demands, while ensuring the reproducibility of our product quality.
The hoses and arteries CoreDux develops, consist of many smaller precision parts that often have to be welded together. In order to reach supreme quality levels, every detail in the manufacturing process counts.
“The base of all our welding knowledge stems from the craftsmanship and over a century of experience of hand welding,”
Ben van Lochem, Process Engineering & QHSE Manager at CoreDux
Manual Gas Tungsten Arc Welding (GTAW) relays heavily on the quality of the welder. At CoreDux, they are all certified according to the NEN-EN ISO 9606-1 norm, guaranteeing the highest standards. “But it is still manual work, so across the board there will be visual differences in the welds,” admits Dave Heesbeen, International Welding Technologist at CoreDux. “Our welders are highly skilled, in the sense that they can adjust to the product at hand. They might, for instance, change the distance between the torch and the product, if necessary. For manual GTAW welding, the tolerances of the preparations are less strict, as we can rely on the know-how of our versatile people.”
However, welders with the right qualification profile are extremely hard to find, especially with the current tight labor market. An additional challenge is that in the last couple of years, CoreDux has been moving more and more to the semiconductor and high-tech industry where its added value is highly appreciated. “This means that many welding jobs have become repetitive,” explains Van Lochem. “Or not very challenging, when you ask our top welders. It requires them to adhere very strictly to a step-by-step plan to comply to the norm. To keep them interested, we need to automize as much as possible, transforming the welders’ know-how to know-why. This way, we have been able to automize our welding processes allowing our highly experienced welders to focus on special weldments needed in complex arteries. And let our engineers focus on more demanding tasks and complex 3D
However, welders with the right qualification profile are extremely hard to find, especially with the current tight labor market. An additional challenge is that in the last couple of years, CoreDux has been moving more and more to the semiconductor and high-tech industry where its added value is highly appreciated. “This means that many welding jobs have become repetitive,” explains Van Lochem. “Or not very challenging, when you ask our top welders. It requires them to adhere very strictly to a step-by-step plan to comply to the norm. To keep them interested, we need to automize as much as possible, transforming the welders’ know-how to know-why. This way, we have been able to automize our welding processes allowing our highly experienced welders to focus on special weldments needed in complex arteries. And let our engineers focus on more demanding tasks and complex 3D constructions and modules.”
Orbital welding
Arguably, the most well-known option in welding automation is orbital welding with a closed head. “Those machines can be operated by people with less welding knowledge,” says Heesbeen. “Still the results will be consistently of high quality, and much more constant than with manual welding.”
Unlike manual welding, in orbital welding the product stands still and the tungsten electrode that creates the welding arc is rotating around the object. Both parts that need to be welded together, are placed in their own cartridge. This way, they are properly aligned and it makes it possible to capture the welding process in protective argon gas. “Without this inert shielding gas, the metal would discolor under influence of the oxygen in the air. Even burning could happen when too much oxygen is present,” Heesbeen explains. Also through the hose a backing gas is guided, to protect the inside of the system from oxidation.
Orbital welding calls for much more preparation than manual welding. The right cartridges have to be selected or developed, and the two pieces have to be positioned with care since corrections during the welding process are not possible. And when there is only the smallest of gaps, the welding torch burns right through. So, CoreDux has an extensive control procedure in place to check and validate every welded component.
Besides orbital welding from the outside, it is also possible to do it from the inside. Sometimes this is necessary because there is minimal to no space on the outside of the product to ‘clamp’ the orbital weld head. However, automated welding on the inside should only be considered as a last resort, since this takes even more preparation in terms of tooling design in the proto phase and has quite some limitations which need to be taken in to consideration when making the product design. In many cases, CoreDux is able to propose re-designs so welding in the more mainstream production methods is an option again.
Another variation of orbital welding is done with an open weld head. The electrode is situated in the center of the exhaust of protective gas that rotates around the object. A second nozzle, coming right after the first, blows away all corrosive oxygen a little bit longer. “With this form of orbital welding, it takes more effort to protect your products,” says Heesbeen. “On the other hand, it gives you more freedom to weld a larger variety of products.”
Automatic robot welding
Orbital welding is a step in the right direction; it allows us to keep our manual welders happy and interested by giving them the specialty welding projects, and it gives us the opportunity to extend our welding capacity. In many situations and for most customers, this is just what is needed. However, some clients are growing even faster. To support their ramp-up and the increasing worldwide demand, scalability in manufacturing is absolutely crucial.
Automatic robot welding is the next level, paving the way for constant high and improved quality and higher volumes, without the struggle to find or train the necessary workforce of additional manual welders.
“Automatic welding is quite similar to orbital welding, except that the welding torch is now driven by a robot. Automatic or semi automatic welding makes sense when you have more standardization and volumes go up. It does, however, have high demands on the preparation of the procedures and on the quality of the supplied components.”
Ben van Lochem, Process Engineering & QHSE Manager at CoreDux
Heesbeen adds: “The welding robot has only one trick up his sleeve. It does precisely what it is told to do. If all goes well and all engineers and operators have done their homework, the robot will deliver perfectly welded hose assemblies or modules.”
To achieve this high quality level, consistent preparation is key. One part of the composition is hold firmly in place by a specially designed gripping tool, that also contains the extractor fans to suck away the welding fumes. The second part is pressed down mechanically on top of the lower part. When the welding robot has completed about two thirds of his round, the mechanical press is removed, creating room for the robot to finish his job.
“The advantages of automatic welding are the constant quality and the fact that you are not dependent on the craftsmanship of your manual welders,” says Heesbeen. “The downside is that you have to prepare everything meticulously, develop special tooling and write extensive software.”
Laser above plasma
CoreDux notices in the market that thinner materials with high precision have to be welded together. So-called CoreDux hybrid hoses, for instance, consist of a plastic liner with a thin stainless steel outer layer. The benefit of these hoses is that they pass on no flow-induced vibrations, securing a laminar flow at high flow speed of the liquid media within the customer application, which is of course essential in advanced semiconductor machines where the vibration transference between critical modules has to be prevent at all costs.
Because of the plastic liner, the temperature during the welding process at the liner should not exceed 40 degrees Celsius, otherwise the plastic material is compromised. CoreDux researched extensively what welding technique would fit the bill. TIG welding, plasma welding and laser welding were all considered. Only with the laser, the temperature remained low enough not to deform the components.
Welding expert Dave Heesbeen: “With the laser beam you can be very precise. The discoloration is negligible and the spot size of tenths of a millimeter enables a very localized power input. This in turn will allow you to weld stainless steel and keep a relatively low temperature of the parts. The challenge is to align the components to perfection because the laser can burn through the thin walls in an instant. Also, additional safety regulations are in order as you are working with a potentially dangerous class 4 laser.”
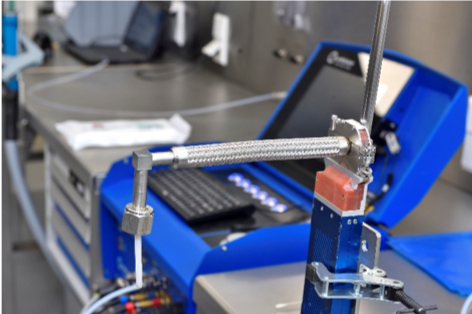
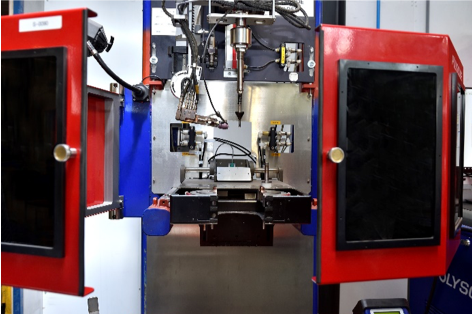
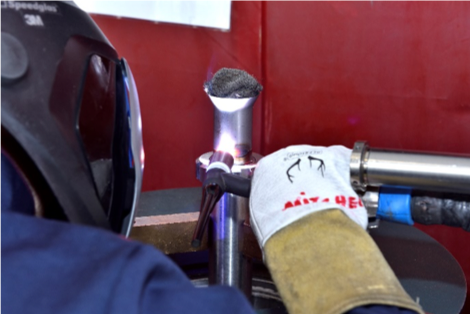
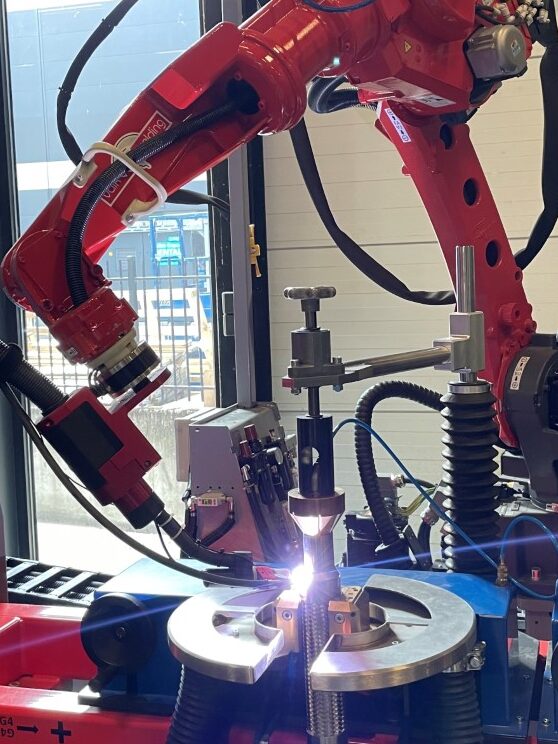